Mercator Medical (Thailand) is a world manufacturer and distributor of high-quality examination and protective gloves made of Nitrile Rubber. We offer gloves suitable for medical, industrial, food and automotive sectors, including gloves for procedures and increased infection risk. We sell our products on the global market mainly under OEM brands of our customers.
Mercator Medical Group
Mercator Medical Group is not only a distributor of medical devices, but also a manufacturer of single-use gloves. The company is one of the few European companies who manufacture gloves in Asia and sell them worldwide.
Currently, Mercator has three of our own production facilities in Thailand. The factories are located in Songkhla province, the southern part of Thailand, with a short distance away from Songkhla and Penang ports, which allows efficient distribution.
About Mercator Medical (Thailand)
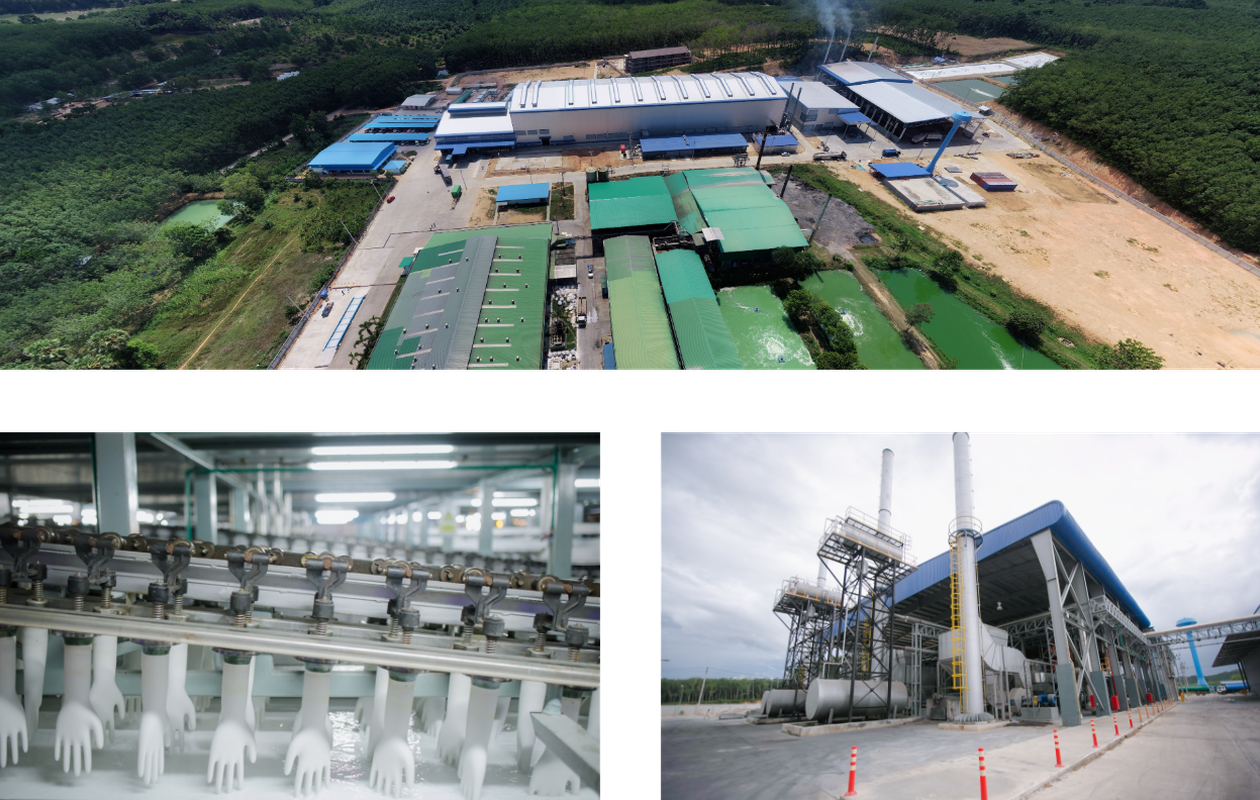
We are proud of our investments, especially in green energy. We invested in waste-water treatment plants, waste-water recycling plants, as well as solar panels and solar farm. Moreover, our wet scrubber for neutralizing the air discharged to the atmosphere is also an investment we put attention on. Our staffs has undergone the ISO14001 training course which is the environment management system to understand and able to manage environmental control more effectively and efficiently.
Certainly, we are responsible for the needs of consumers, and we follow the industry’s latest trend. We constantly look for new manufacturing solutions to keep on growing consistently, which transcribes to our broad portfolio of examination and specialty gloves classified at Class III Personal Protective Equipment (PPE). We offer our products globally and Mercator’s assortment is shown at major industry events.
Mercator Medical (Thailand) meets ISO management system. Our company goes through various audits to optimize our production process on an ongoing basis.
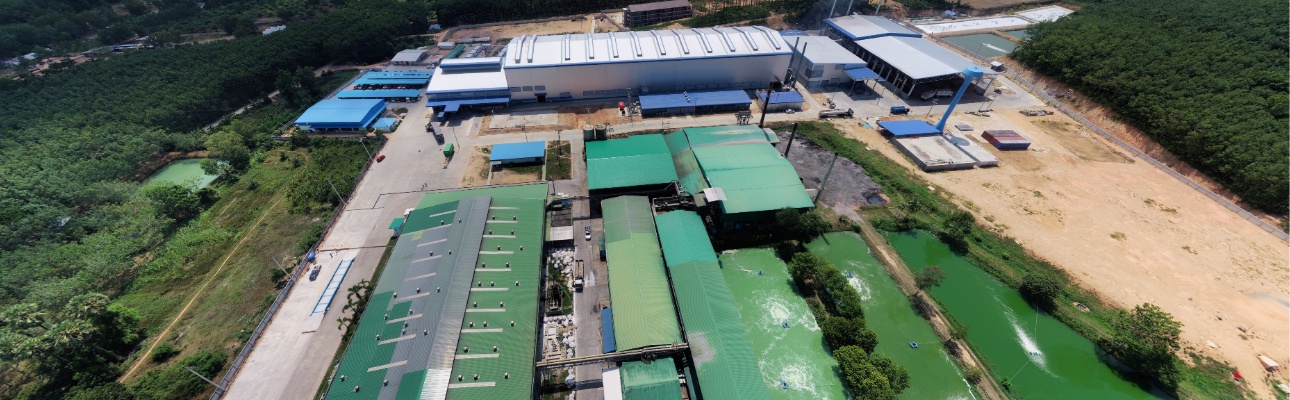
European factory in Asia
The Management Board of Mercator Medical (Thailand) consists of qualified specialists from Thailand and Poland. Together, we make up a multicultural organization, combining the highest European management standards, customer service and quality, with Asian manufacturing know-how. Thus, we have our own grounds and do not depend on external suppliers. Mercator Medical (Thailand) is the first Polish investment in Thailand with a consistent development, aiming to meet the growing demand for single-use gloves.
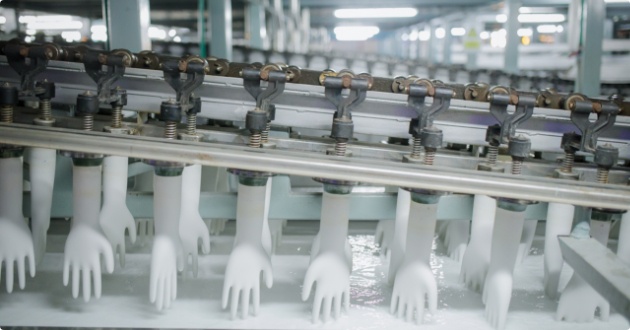
Area
Our whole land area including the three factories and surrounding facilities is 28 hectares (282,944 square meters), while the area of three production halls is a total of 1.6 hectares (16,060 square meters)
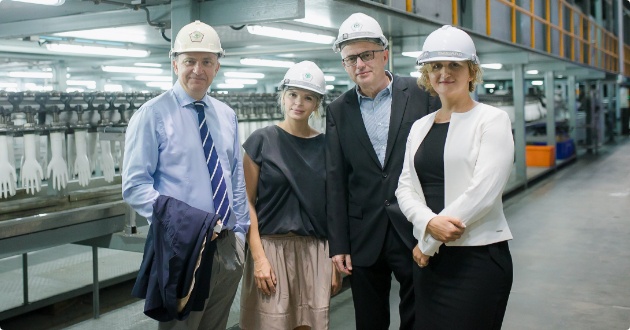
Part of the Mercator Medical Group
Mercator Medical is a valued and recognised European distributor of medical and protective gloves. Products manufactured by Mercator Medical (Thailand) Ltd. are channelled to the distribution network of the Mercator Medical Group. The Thailand factory is the first Polish investment in that country, which is constantly developing – not only in terms of the production scale, but also its range. All to meet the growing demand for single-use gloves.
Raw material
Our essential raw material used in producing gloves is Nitrile Rubber or NBR.
Nitrile
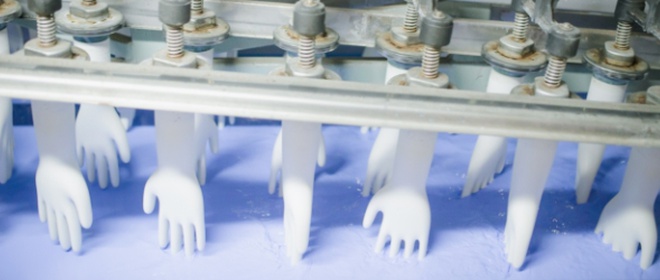
Nitrile, also known as nitrile butadiene rubber (NBR), is a material composed of organic chemical compounds and an essential raw material used for producing gloves.
- Nitrile gloves are latex-free, making them safe for people with allergies.
- Nitrile has very low levels of chemical vulcanization accelerators, therefore, gloves made of this raw material are much less likely to cause type IV allergies.
- Nitrile gloves are more durable than latex gloves.
Latex
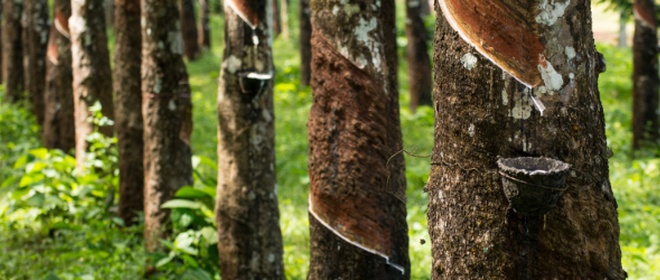
Latex is manufactured from natural rubber which is extracted from rubber trees. In the morning, V-shaped incisions are made on the tree stems. Below these incisions, containers are placed to collect the milk. Latex is an entirely natural, biodegradable and environmentally friendly raw material.
- Proteins contained in latex may cause type I allergy – to minimise the risk of symptoms, some of the latex gloves manufactured by Mercator Medical Thailand are covered with a skin-safe polymer coating.
- Latex gloves are very flexible and fit comfortably on the hand.
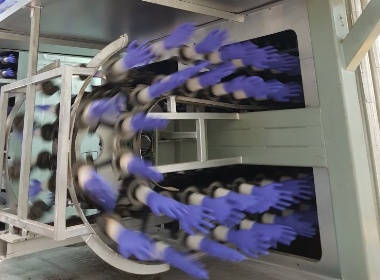
The history of Mercator Medical (Thailand)
Mercator Medical (Thailand) was established in 2006. In the same year a small gloves factory with an annual capacity of 480 mil gloves was purchased by the company. The Mercator Medical factory was at the same time the first industrial investment of the Polish company in Thailand.
In 2015, the expansion project of the first factory was completed. It allowed to increase annual production capacity to 1.3 billion gloves.
In 2016 a green field project was launched to build a new production facility able to produce 1.9 billion highest quality NBR gloves per annum. Project was completed in 2018 and cost 30 million USD.
Thanks to continuous investment in production facilities and environmental protection, the factory can boast the most modern production lines in the region. The company is recognized worldwide and presents its assortment at the most important medical fairs.
Mercator Medical (Thailand) Ltd. is regularly audited by notified and accredited bodies. It has an international GMP (Good Manufacturing Practice) certification as well as ISO 9001 and ISO 13485 certification, which we have been certified since May 2007and a certificate of the Thai Food and Drug Administration. Our products conform to the ASTM and EN standards and have an FDA 510(k) and CE certificate.
In 2019, Mercator Medical (Thailand) Ltd. implemented the SA8000 standard – the most well-known social responsibility standard based on the guidelines of the International Labour Organization (ILO), Universal Declaration of Human Rights and the United Nations Convention on the Rights of the Child. It is applied by companies which focus on the rights and well-being of their workers.
In addition, in 2019 Mercator Medical (Thailand) Ltd. obtained the TLS (Thai Labour Standard) certificate, which is the local equivalent of a social responsibility certificate.
In 2020, another green field project was started. As part of the project, we built infrastructure to produce high-quality specialty gloves, a modern biomass boiler house, an RO installation for water recirculation with a capacity of 1500m3 and a solar farm with a capacity of 4.7MW. Thanks to new investment, Mercator Medical Thailand will be able to produce more than 1 billion highest quality specialty gloves per annum. Thanks to investments in renewable energy sources, most of the energy used in the production of gloves will come from zero-emission sources.
Nitrile gloves manufacturing process
Most nitrile gloves are manufactured in the same process so why do our gloves stand out from the other manufacturers? We have multiple stages of control from choosing the right raw material suppliers to final control of finished products. We select only reliable and authentic raw material suppliers. Once the raw material is being delivered to our facility, we check the quality of the raw materials before we accept them. During compounding stage of our preparation of raw materials, our lab checks the quality of the raw materials. Only when it is accepted and passes our criteria, we should dispatch them onto the production line.
Moreover, another crucial criterion of our checking is the quality of the water being used for preparing the compounding materials and in the production line. We only use water that is clean and soft enough for the process which is why our gloves will not create type IV allergies. Not only because of the fact that we use Nitrile Rubber, but also because any excess chemicals on the gloves have already been washed away before the gloves come out of the production lines.
Environment
We pay full attention to the environment and our customers. We are committed to producing high quality products in our environmentally friendly facilities. We have waste-water treatment and waste-water recycling plants, solar panels, and solar farms. During peak days, our solar panels and solar farm cover all the electricity used in our three factories. Furthermore, we also have 2 rainwater ponds to collect rainwater during the rainy season which can then be used for some cleaning activities. In the last waste-water treatment pond before the water is being discharged into the river, we keep hundreds of fish to ensure that our water is clean enough for sea lives to live in. Our customers can rest assured that the products they buy from us are produced in an eco-friendly environment in which they are also supporting the environment and helping save this earth.
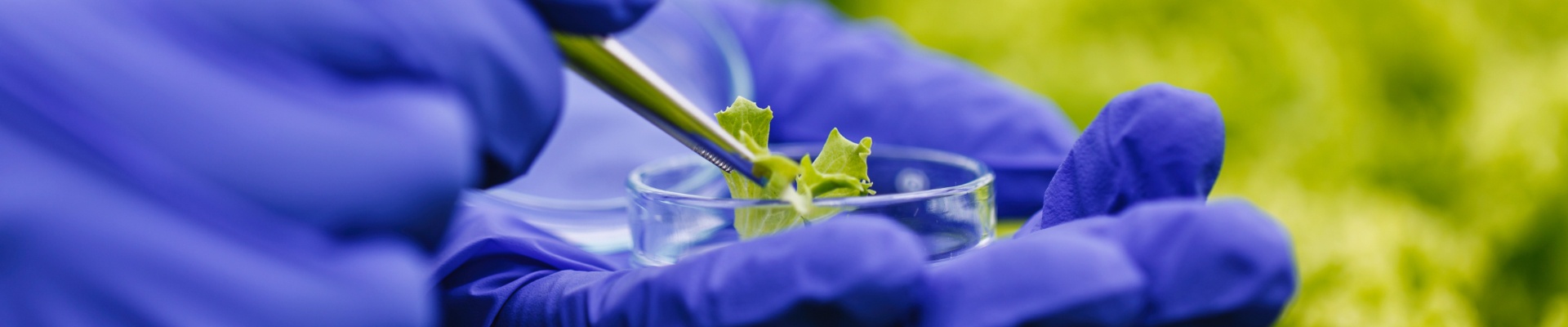
Solar
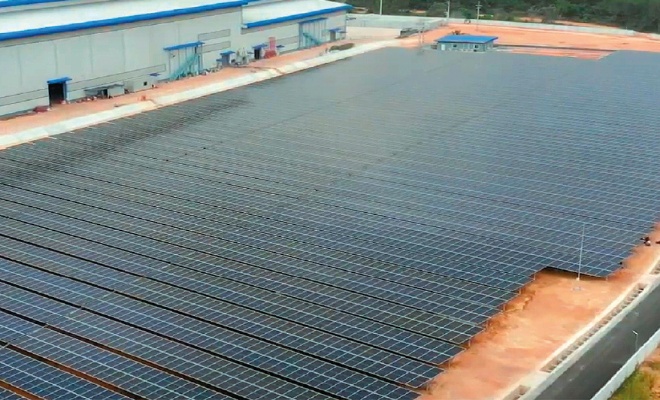
As stated previously, we care about the environment. We believe that we are the only Thai gloves manufacturer with a solar farm, producing green energy for electricity being used in producing gloves. Customers can be certain that if they buy gloves from us, they are supporting a company that cares truly about the environment and the earth. Customers are also indirectly supporting the environment. A part of the gloves bought is being produced by clean, green energy. Support Mercator, support the Earth.
In Plant 2, we have solar panels installed on the factory roofs. The capacity is around 1.4 MW. The daily average usage is around 5,000 – 6,000 kWh, depending on the weather condition.
For the solar farm that is currently under construction but will be completed soon, the capacity is gigantic, at around 4.7 MW. The electricity usage plan for all 3 plants is around 5,616,000 kWh per month, which is up to 13% is powered by green energy.
Biomass energy 100% from nature
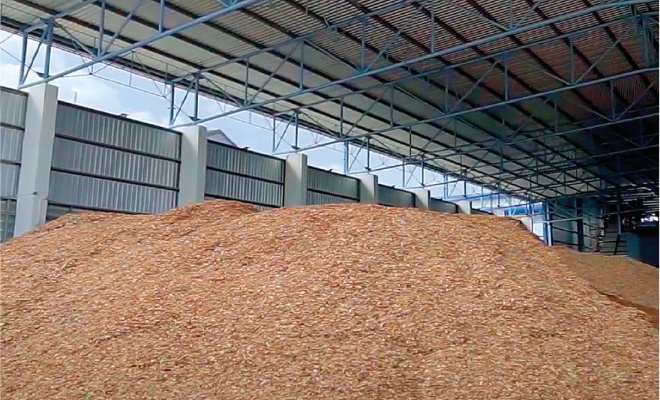
100% of heat energy used for production process in Mercator Medical Thailand is generated from biomass. Biomass has been promoted as a carbon-neutral energy source by industry, some countries, and lawmakers on the basis that the emissions released by burning wood can be offset by the carbon dioxide taken up by trees grown to replace those burned, therefore, energy produced with biomass is 100% clean. Most of the biomass used in Mercator Medical Thailand comes from controlled rubber trees plantations. Plantations renew trees every 15-17 years. Old trees are used to produce timber. Timber waste is used to produce woodchips and converted to fuel. Our Thermal Oil Heater (TOH) contains a gigantic cyclone to trap any dust produced after burning biomass. Inside of the cyclone consists of hundreds of small cyclones inside which filters all the dust and exhausts so that no dust flies up to escape the cyclone. Only clean air can escape the cyclone. Anything that is heavier than air is then blown through these multi-cyclones downwards and drops into the tank. Once the tank is full, our external supplier will then take the dust. Some of the dusts are mixed in cement, some are made as fertilizers, and many are used as land filling.
Waste-water treatment and recycling plants
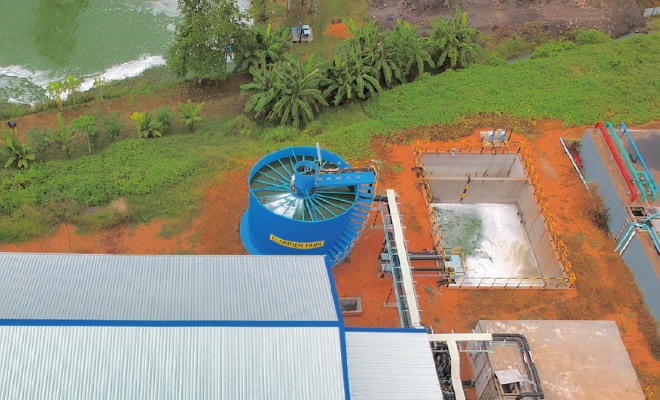
As mentioned, we have a waste-water recycling plant which currently has an operating capacity is 3,000 cubic meters per day with 55-60% efficiency, meaning we can recover up to 1,800 cubic meters of water per day. The technology used are clarifier, ultrafiltration, and reverse osmosis. Waste-water that leaves from the process goes through various bio-treatment ponds and mechanical separation plants. Discharged water parameters are under continuous, automatic control monitored by the Biological Oxygen Demand (BOD) which is the oxygen level the waste-water needs for recycling. This is an online system controlled by the Ministry of Industry. The parameters results are sent to the Ministry of Industry every 15 minutes which they can monitor and continuously check if our parameters pass the requirements
Moreover, we are also running a second phase of the waste-water Recycling Plant expansion. Once expansion is completed, the total capacity of the waste-water will reach 6,500 cubic meters per day with the efficiency up to 55-60%.
With the waste-water recycling plant expansion, this will reduce the discharged water to the public canal to up to 55-60% and the recycled water will be used in the production process. To ensure that the water discharged to the public canal is safe and clean, we are keeping hundreds of fish in the final pond. Our fish are swimming well and healthy in our water and we will continue to increase the number of fish in the pond.
Air pollution controlled by Wet Scrubber
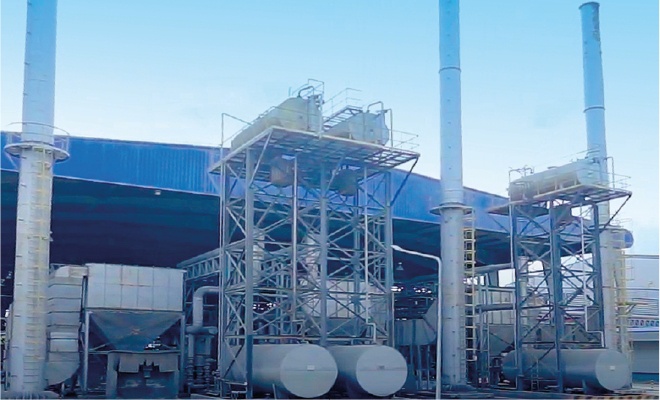
Our factories another technology called the scrubber. Inside of the scrubber contains a water spray that sprays water to trap the dust so that it does not fly up in the sky. Both our cyclone and scrubber exist to ensure that the air we release is according to the standard controlled by a certified external party which comes to our factory to regularly measure the results every 6 months. There are different parameters that are tested by an equipment called Console Stack such as Total Suspended Particulate (TSP or easily known as the dust), Sulfur Dioxide, Nitrogen Dioxide, Carbon Monoxide, and Opacity which our results are always a pass within the control, meaning that the quality of the air we release is clean.
Standards
Our claim in being committed to producing high quality products is confirmed by various certifications and standards we meet.
We are regularly audited by notified and accredited bodies. We have ISO 9001, ISO 13485, Good Manufacturing Practice (GMP) certifications, as well as Thai Food and Drug Administration certificate. Our products conform to ASTM and EN standards, along with having FDA 510(k), CE, UKCA marks for medical products, while for PPE, we contain CE2777 and AB0321 marks.
Not only do we meet product standards, but we also pay attention to the well-being of our employees. In 2019, we have undergone the SA8000 audit and implemented this standard in our system. The SA8000 standard is the most well-known social responsibility standard based on the guidelines of the International Labour Organization (ILO), Universal Declaration of Human Rights and the United Nations Convention on the Rights of the Child. We are confident and can fully confirm that none of our employees is being mistreated. Moreover, we have 4 hostels for our foreign and Thai staffs to live in with free of charge with an area for our staffs to play their most favorite sport, which is Speak Takraw, also known as ‘kick volleyball’, which is commonly played in Southeast Asia, including Thailand and Myanmar, where most of our staffs come from. Currently, there are over 1,000 employees, mainly from Southeast Asia.
Employee rights
We exercise respect and professionalism when it comes to our work ethics. The Group’s staff policy is based on ethical values, a system of professional competences and open communication. Our factory is distinguished by American employment standards. We work in a system involving three shifts and eight hours of work. Our business is continuously audited, and as a result, we are constantly improving our processes and maintaining the quality of our products, which has earned us recognition among customers across all continents.
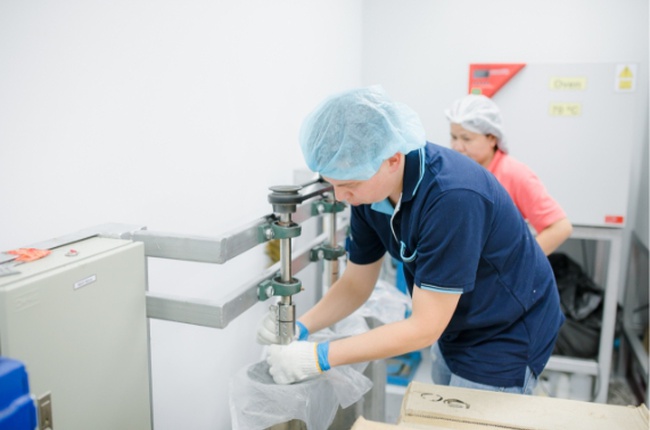
Production quality control
Each batch of gloves manufactured at Mercator Medical Thailand goes through five steps of quality control processes which ensures high quality products are being produced, checked, and shipped out. Our procedure complies with the ISO standard, of which we are regularly audited to ensure that we are always up to the standard. We have incoming raw materials quality control from our internal lab, in-process quality control of the gloves every hour, form lot control once the gloves reach one lot which consists of 60,000 pieces of gloves, we perform water tightness test (WTT) or air pump test (APT), depending on the destination country, we check physical properties, dimensions, weight, thickness of the gloves, and finally, before the gloves is going to be shipped out, we have a pre-shipment control to check all of the crucial parameters.
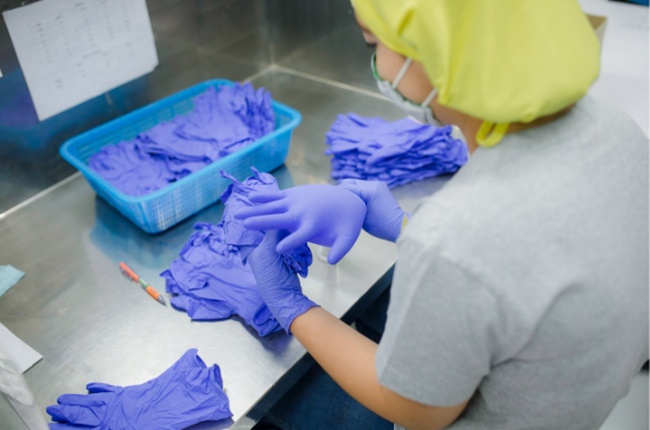
Certificates
The quality of our products and procedures related to employee rights is proven by the certificates we have received:
International Organization for Standardization ISO 9001/ISO 13485
International Organization for Standardization 9001 and 13485 – the Quality Management System for Medical Devices developed in accordance with the requirements of ISO 9001, ISO 13485 is an international standard containing requirements for medical devices intended to guarantee the highest quality of products and their compliance with the law and customer expectations.
EU type-examination certificate
EU-type examination certificate – EU-type examination is a procedure whereby a notified body ascertains and attests that the product, including its technical documentation and relevant life-cycle processes, as well as a representative sample of the envisaged product, complies with the relevant provisions. EU type examination certificate is for Personal Protective Equipment (PPE), which Mercator Medical Thailand’s product is classified as Category III.
NFPA 1999 Standard on Protective Clothing for Emergency and Ensembles for Emergency Medical Operations
As far as we are concerned, Mercator Medical Thailand is the only Thai manufacturer qualified for NFPA 1999 standard which is the standard of protective clothing and ensembles for emergency medical operations. NFPA 1999 contains a significantly high standard with strict auditing rules and regulations which we see as challenging and our gloves are able to meet the requirements of this standard.
CE marking
EU regulations require the use of CE marking. The CE marking indicates that the product can be legally sold in any EU country, therefore, the gloves must be marked with this symbol.
UKCA marking
Like CE marking for EU countries, UKCA marking is for Great Britain. We are registered with UK’s NHS which allows us to have UKCA marking.
Good Manufacturing Practice (GMP)
The GMP rules ensure high quality and the highest purity of the materials used to produce medical and protective gloves, and full control of the origin and quality of raw materials and the entire manufacturing process.
Social Accountability 8000 or SA8000
This standard covers human rights and employee rights. The element at the heart of SA8000 is the concept of Corporate Social Responsibility (CSR). It considers the social and environmental aspects of company management and all other factors that may affect the employee of a given company. Implementation of this standard makes business ethical and employee-friendly, which Mercator Medical Thailand pays full attention to.
Thai Food and Drug Administration or Thai FDA
Thai FDA is responsible for the protection of the consumer's health and safety by ensuring the quality and efficacy of health products.